Crafting Precision: Exploring Custom Workholding Solutions
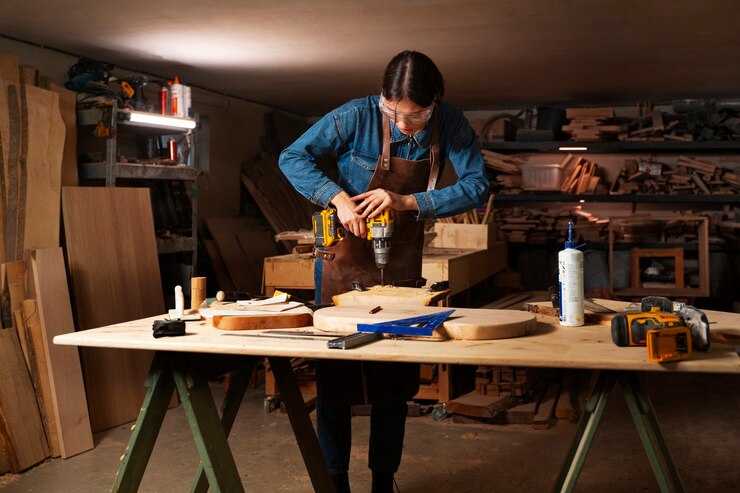
In the world of manufacturing, efficiency and precision are paramount. Custom workholding solutions play a crucial role in achieving these goals. By securely holding parts during machining, custom workholding ensures accuracy and repeatability. This article delves into the significance of custom workholding, its benefits, and how it can be tailored to meet specific needs.
The Importance of Custom Workholding
Custom workholding solutions are essential for optimising the machining process. Standard workholding tools often fall short when dealing with unique or complex parts. Custom solutions are designed to fit the exact dimensions and requirements of each part, ensuring a secure hold and precise machining. This not only enhances product quality but also reduces waste and rework.
Benefits of Custom Workholding
-
Enhanced Precision
Custom workholding ensures that parts are held securely in place, minimising movement and vibration. This results in higher precision and consistency in machining, leading to better product quality.
-
Increased Efficiency
Custom workholding tools are designed to streamline the machining process. They reduce setup times and improve the overall workflow, enabling faster production cycles and increased output.
-
Reduced Waste and Costs
By ensuring accurate machining, custom workholding reduces the likelihood of errors and defects. This leads to less material waste and lower costs associated with rework and scrap.
Tailoring Solutions to Specific Needs
Custom workholding solutions can be tailored to meet the unique requirements of different industries and applications. Whether it’s for aerospace, automotive, or medical device manufacturing, custom workholding can be designed to accommodate various shapes, sizes, and materials. This adaptability makes it an invaluable tool for manufacturers looking to enhance their production capabilities.
Case Study: Custom Workholding in Action
Consider a manufacturer producing complex aerospace components. Standard workholding tools were unable to securely hold the intricate parts, leading to inaccuracies and delays. By implementing custom workholding solutions, the manufacturer was able to achieve precise machining and reduce production time significantly. This case highlights the transformative impact of custom workholding on manufacturing efficiency and product quality.
Choosing the Right Custom Workholding Solution
When selecting a custom workholding solution, it is important to consider the specific requirements of the machining process. Factors such as part geometry, material, and machining operations must be taken into account. Collaborating with experienced engineers and manufacturers can help in designing and implementing the most effective custom workholding solution for your needs.
Conclusion
Custom workholding solutions are essential for modern manufacturing, providing the precision and efficiency needed to produce high-quality products. By tailoring workholding tools to specific needs, manufacturers can optimise their processes, reduce waste, and increase productivity. Investing in custom workholding is a strategic move that can yield significant long-term benefits, ensuring that your manufacturing operations run smoothly and efficiently.
In a world where precision and efficiency are crucial, custom workholding solutions stand out as a key component of successful manufacturing. They not only improve the quality and consistency of products but also contribute to overall operational excellence.